Sustainability at Gerber & Co
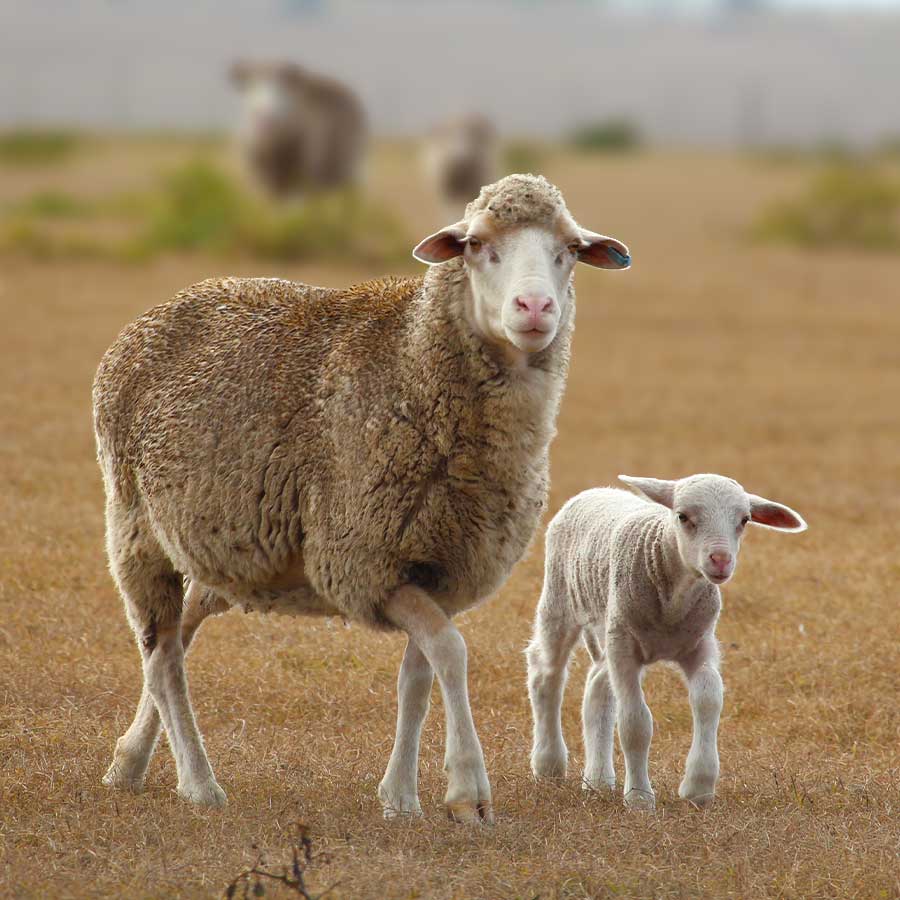
Sustainable Cape Wool Standards
Animal Welfare
We, Gerber and Co, as the only supplier of wool for our knitted garments, take good care of our sheep.
Gerber and Co have committed us to adhering to the Sustainable Cape Wool Standards. This means we have committed ourselves to high animal welfare practices and environmental custodianship. For example, we manage our sheep in line with the Five Freedoms. In addition, the entire South African sheep population is mulesing free, another big commitment and dedication us and other wool growers made to ensure a happy and healthy life for our sheep.
You can read more about the Cape Wool Standard by clicking on the button below.
The Five Freedoms
-
Freedom from hunger and thirst
-
Freedom from discomfort
-
Freedom from injury and disease
-
Freedom to express normal behaviour
-
Freedom from fear and distress
-
Materials
Wool – a sustainable fibre.
One of our core beliefs is that wool is a sustainable fibre. Wool and products made from wool, in general, are already a sustainable choice. We have already written several blog posts explaining how and why wool is a sustainable fibre, and you can read more about it below.
-
Traceability
We continuously strive to reduce our environmental footprint within our own supply chain therefor most of the vertical supply chain for our wool garments is owned by Gerber and Co, including the sheep and the land it grazes on. Making us a ‘one of a kind’ operation. Our offices, wool scouring plant, knitting and embroidery facilities and distribution centre are all under one roof.
Our Certifications
Gerber & Co Supply Chain
Step 1 - Wool grown in Namaqualand, South Africa
All Gerber and Co wool garments are made of South African merino wool, more specifically wool from our sheep that grazes on our Namaqualand farm.
We shear the sheep’s wool in springtime and send their wool to the Gerber and Co Scouring (washing) plant in Paarl. During this time the wool gets tested by the Wool Testing Bureau South Africa to define the different qualities of the wool such as fineness (micron), strength, length, colour etc. All the testing results are documented on a wool test certificate.
Step 2 - Designed in Paarl, South Africa
We design all our garments in-house in Paarl, South Africa. Once the designs are ready, we specify all the technical details and send them to Gerber and Co Knitting to create samples. After a few iterations, all design details are sorted, and we are ready to place an order.
Based on our order the knitting facility calculates how much wool is needed to fulfil the order.
Step 3 - Wool Processing – Paarl, South Africa
At Gerber and Co Scouring, our wool gets washed. In detail, this means that our wool is put into large pools of water and soap to wash the wool grease as well as the dirt, sand and grass from the field out of the wool. The wool grease gets extracted from the water to be used in cosmetics and beauty products. The dirt, sand and grass get filtered out to be used as a fertiliser. The water that has been used is filtered and cleaned to be reused at other parts of our operation.
After washing (also called scouring) of the wool, the wool gets dried in huge ventilation boxes. After this stage we transport the clean wool to a combing, spinning and dyeing facility.
Step 4 - Wool Processing – Worcester, South Africa
At this facility the wool gets carded. This is a process where the individual wool fibres are being straightened and aligned. The outcome of this process is a carded sliver. This carded sliver is then being fed into a drawing machine which further paralyses the wool fibres. Typically, the wool passes three times through the drawing machine. The next step is the combing machine. The combing machine removes short fibres, any vegetable matter and any knots that may have occurred. The last step in the process is the gilling machine. This process removes any wave patterns that got imprinted during the combing and regulates the actual weight of wool per meter of the sliver. The sliver is the final product, also called a wool top, of this processing step which is the basis for the next step, the spinning process.
During the spinning process, our wool tops are spun into yarn. Basically, what happens is that the thick wool top gets pulled more and more into a very thin but strong thread. The yarn is then dyed into the different colours we have chosen for our new collection.
Step 5 - Garment Knitting – Paarl, South Africa
Once the yarn is dried and ready it is transported to our Gerber and Co Knitting facility that is also at our scouring plant in Paarl. The different panels for our garments get knitted by machines and thereafter sewn or linked together by hand using machines. Some of our garments get branding sewn onto them and others get embroided with our quiver tree logo. And this happens at the next step.
Step 6 - Garment Embroidery – Paarl, South Africa
Gerber and Co Embroidery is located next to the knitting facility in the same room. Our garments get embroided here and the final quality checks are being done here.
Step 7 - Distribution Centres – Paarl, South Africa
We store all our garments on-site at our office in Paarl and at our Gerber and Co retail outlet in Simondium, Paarl. Once your order comes in one of our team members collects the items you ordered and ships them off to your shipping address.